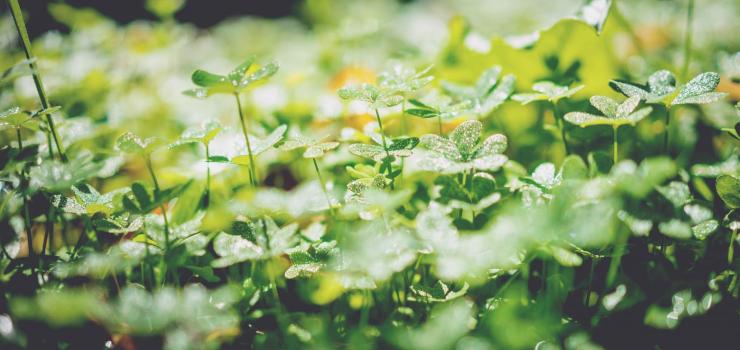
Saving Energy and extra safety for the CPR15.2 guideline by using the MACView® gas measurement system 10 September 2012
The CPR15.2 guideline (Committee Prevention of disasters) is a Dutch guideline that says, in (heated) warehouses for chemical storing an air refreshment factor of 5 is needed. These refreshment factor keeps the concentration of gasses low and prevents arising of vapours, these vapours can cause explosion danger. The refreshment factor is generally an expensive item. Especially in the winter when the warehouses are heated or in the summer when the warehouses are cooled are the costs an alternative worth.
EMS can solve this problem by connecting their gas measurement system to the ventilation system. We only use a ventilation system if this is really necessary. It is possible that the ventilation system has several stages of detection at start-up or in the adjustments. When the ventilation only starts in cases of a high concentration caused by leakages, spill or other emergencies, the costs of the energy to heat or cool the warehouse degree. Even if a heat changer is used the costs are always higher.
A main point of the gas detection or vapour detection is the preventive side of it. Normally many warehouses are provided with fire protection installations. In generally the extinguish installation starts to late (because a fire alarm needs a fire to give his alarm). It is easily by using the MACView® gas detection system to measure the fire risk and take the first steps to prevent it. A fire is the next stage. For a fire starts, the concentrations should increase to high levels and an inflammable source is needed. Burnings in large warehouses are very dangerous because there is always a great risk of an explosion. These dangers can extremely degree when using the MACView®.
Stock-taking
Before the implementation, it is needed to look to several factors. It must be known which gasses are present. What are the properties of them? Are there liquids, gasses or vapours? Are they detectable? What are the flash points or the flame points? Are there pressed gasses? How many are there? Are there subjects which act as a catalyst, or extinguish they each other? For al these subjects, it is needed to do stocktaking. Because of this stocktaking it is possible to determine which gasses explicit can be detected and which gasses and vapours cannot be detected.
Position-finding
Important facets in the definition of measuring with gas detection systems are:
- Place or location (Overlapping areas and cost effective distribution of the sensors.) (More then 1 sensor on a control unit? Placement high or low to the ground? Do the gasses and or vapours lift off or do they lower?)
- Number of fixed gas detection systems. (Distribution of overlapping areas)
- Way of measuring.
- Rate of reliability of the device. (Fail-safe? Connection with the fire department? Speed of detection?)
- Ventilation air stream connected to the correct gas detection location.
- Environmental conditions. (Temperature, humidity and possible risk of explosions (Ex-zone))
- Robustly and maintenance. (In use and also cost technical)
Control of gas detection systems
The right control of gas detection systems is an art. The best way to control is that all systems can be controlled and read from a central point (in the office, security, doorkeeper or at the fire department). If the system gives more information then only gas concentration, it is possible to give indicative conclusions from the control centre. In case of an alarm it is possible to send: temperature, relative humidity and fire mention points. With this information it is possible to make a better overview of the local situation. In closed warehouses, the control centre can give information to the emergency services of the situation inside the building. The easiest way to control al these nodes is to use a multi-node network (for example Ethernet or something like that.) with this it is easy to switch from one system to the other system and view the individual parameters of each system. Fast and convenient arranged 3D charts can show the places where the possible leak is. In combination with a database the data can be stored. A database can also provide advice about the stage or how the emergency plan should be used. Another option is to let the database choose if the building should be ventilated or not. Is it allowed to ventilate in case of a fire alarm? (Stop the oxygen supply or do ventilation?) EMS has several systems (hardware en software) that can give a solution in these circumstances. The systems are made of modules. The gas detection systems can send signals in the range from a simple 0-20mA until a complete web-based intranet application. Al these systems have commonly that these are systems use international standards and communication protocols.
Maintenance
The maintenance is a factor whereupon to make the biggest revenue. There are several choices to consider about, for example: detection accuracy, costs en durability of the sensors. The calibration is very important. Even if the sensors are seems to be good, it is necessary to check the sensors periodically. This check can be done by the system itself or it can be a complete calibration in a workplace. The simplest way is to calibrate the sensors at the location. If this is almost impossible through some circumstances, it is always possible to disconnect the sensors and calibrate these sensors in the workshop. Also for this counts, the universal nature of the devices is very important for the ease of the job and for the right interpretation.